It is important to consider all aspects of listed wiring vs field wiring to ensure safety, efficiency, and compliance with electrical cords. Understanding their key differences will allow you to have a smooth installation without compromising all necessary standards.
In this article, we will see a few essential tips that will help you decide between listed and field wiring.
Understanding Listed Wiring vs. Field Wiring
Listed wiring, also known as pre-manufactured wiring systems, is factory-assembled and tested to meet specific safety and quality standards. For EMF-related safety, you can rely on home bundles from EMF safety solution providers for both wiring systems. Also, they are UL-listed or certified with other reputable testing organizations. Thus, they comply with strict electrical code requirements.
In contrast, field wiring refers to on-site electrical wiring, where conductors, conduits, and connections are manually installed and terminated during the construction phase. Both listed and field wiring have their advantages, but choosing the right option depends on factors such as project complexity, compliance needs, and installation environment.
1. Consider Electrical Code Compliance
Electrical code compliance is a fundamental factor in selecting between listed and non-listed wiring. Listed wiring systems are pre-approved by testing laboratories, simplifying the approval process with inspectors. Since factory-assembled wiring adheres to predefined safety standards, it reduces the likelihood of installation errors and code violations.
On the other hand, field wiring requires strict adherence to local and national electrical codes during installation. If your project demands extensive customization, field wiring may be necessary, but it comes with added responsibility for compliance verification.
2. Evaluate Installation Speed and Labor Costs
Wiring installation standards play a significant role in determining project timelines and labor costs. Listed wiring systems offer a faster installation process since they arrive pre-configured with connectors, enclosures, and necessary terminations. This reduces labor costs and minimizes error as it doesn’t need any stripping or assembling.
Conversely, on-site electrical wiring involves a more time-consuming process where electricians must measure, cut, and connect wires manually. If project deadlines are tight, factory-assembled wiring is a more efficient choice.
3. Assess Project Complexity and Customization Needs
Projects with straightforward wiring requirements can benefit from listed wiring systems due to their plug-and-play nature. These systems work well in standardized installations, such as commercial buildings, modular homes, and prefabricated structures, where uniformity and efficiency are essential.
However, some installations require highly customized electrical layouts that pre-manufactured wiring systems may not accommodate. In such cases, field wiring is a better choice. It allows electricians to tailor the wiring paths to space-specific needs. So, before choosing the wiring evaluate what your project demands.
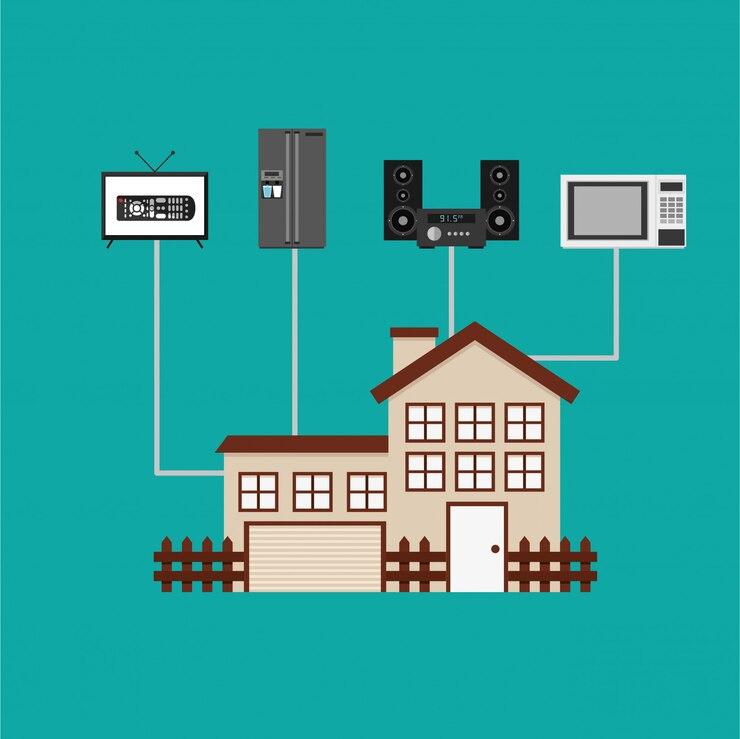
4. Weigh Safety and Reliability Factors
Safety is a top priority in any electrical installation. As electricity is involved, EMF radiation hazard is a must, in such cases using protection like a home harmonizer can be really helpful.
Field wiring, while safe when installed correctly, carries higher risks if not done by skilled professionals. If safety and reliability are paramount, listed wiring offers a more dependable solution.
5. Compare Cost Implications
Listed vs. non-listed wiring costs vary depending on project size, labor requirements, and material expenses. Listed wiring systems may have a higher upfront cost due to manufacturing and certification, but they often reduce overall expenses by lowering labor costs and minimizing rework due to compliance failures.
Field wiring may seem cost-effective initially, especially for small-scale projects, but unexpected delays, labor costs, and potential code violations can add up over time. Conducting a thorough cost analysis based on project scope can help determine the most economical choice.
6. Factor in Future Maintenance and Upgrades
Maintenance and scalability are essential considerations in wiring installation standards. Listed wiring systems typically come with standardized components that make future upgrades easier. Since they follow uniform designs, replacing or expanding the wiring system is more straightforward.
Field wiring may require more effort during maintenance due to its custom nature. Identifying and troubleshooting issues can be time-consuming, especially if wiring routes are complex or poorly documented. If your project anticipates frequent modifications or expansions, the 1-listed wiring is a more convenient choice.
Making the Right Choice
Choosing between listed and field wiring depends on several factors, including compliance requirements, installation speed, customization needs, safety considerations, cost, and future maintenance. Factory-assembled wiring offers efficiency, safety, and ease of compliance, making it ideal for projects with standard wiring layouts.
On-site electrical wiring provides flexibility but requires careful planning to ensure code compliance and safety. In terms of safety considering EMF threats is also important, so relying on EMF solutions can be helpful in this regard.
By evaluating these key aspects, you can select the best wiring method for your project, ensuring a reliable and efficient electrical installation.